Patent granted for use of oxalic acid powder for debinding POM feedstocks
August 14, 2023
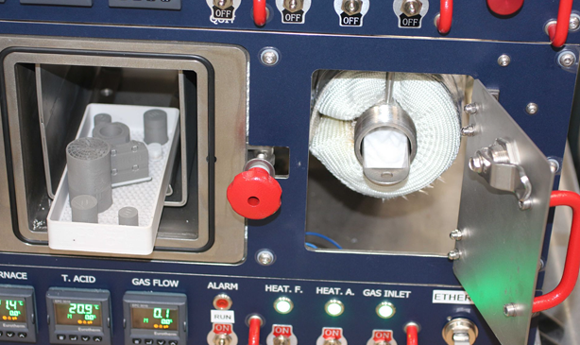
XERION Berlin Laboratories GmbH, Berlin, Germany, has announced a patent for a new method for catalytically debinding polyoxymethylene (POM) based feedstocks, such as BASF’s Catamold® for Metal Injection Moulding (MIM) or its Ultrafuse® filaments for Additive Manufacturing, using oxalic acid powder.
Both the Catamold and Ultrafuse materials see widespread use in MIM and metal Fused Filament Fabrication (FFF, also known as filament-based Material Extrusion (MEX)) thanks to the reduced time required for catalytic debinding compared to solvent based debinding methods. This is especially the case for parts with larger wall thicknesses and allows for faster batch processing and higher throughput for manufacturers.
Typically, nitric acid in varying concentrations is used to catalytically debind POM-based feedstocks in order to remove the polymer backbone before sintering. While advantageous for the aforementioned reasons, the challenges that nitric acid poses with regard to the environment, as well as safe handling, are well known within the industry. The new catalytic debinding method from XERION, used in its Fusion Factory XS system, alleviates these issues by using oxalic acid rather than nitric acid.
Oxalic acid is naturally occurring, found in various plants, leaves and even honey. As opposed to nitric acid, which is stored as in liquid form, oxalic acid can be stored as an odourless powder, which is safe to handle. It was stated that the amount of oxalic acid required for catalytic debinding in the Fusion Factory XS is comparable to the amount of oxalic acid that one would find in a handful of rhubarb leaves. The byproducts from the use of oxalic acid in the Fusion Factory XS system from XERION Berlin Laboratories present no harm to the environment and processing time is similar to debinding with nitric acid.
The Fusion Factory XS is an all-in-one metal FFF Additive Manufacturing, debinding and sintering system, built into multiple compact Pelican™ cases that are easily transported and can endure rugged conditions. The debinding unit and sintering furnace are housed together within one Pelican case, where the catalytic debinding unit consists of two independently heated interconnected chambers. Within the box chamber, ‘green’ AM or MIM parts are placed where they are heated to an elevated temperature.
The other chamber contains a pre-prepared oxalic acid cartridge, which is then heated so that the oxalic acid sublimates and is transported to the chamber with the green parts. The remnants of moved backbone polymer are then safely burned off within an electrical burner, therefore posing no risk to anyone in the vicinity of the system.
The sintering furnace can achieve temperatures up to 1,550°C within an argon/forming gas atmosphere. The furnace utilises a cold-wall system, cooled by a chiller housed within a separate Pelican case. During thermal debinding, the same electrical burner as the debinding unit is used.
The custom-made dual extruder AM machine, specifically designed for the processing of powder-filled POM filaments, is housed within its own Pelican case. Filament is stored on compact spools that move on an independent linear rail, as part of a separate patent belonging to XERION. The overall solution therefore lends itself well to BASF Ultrafuse stainless steel in combination with its ceramic support interface.
XERION stated that it has considered the safety and environmental impact in every aspect of the Fusion Factory XS system, with its compact and transportable footprint enabled by this new method of catalytic debinding using oxalic acid.
Download Metal AM magazine
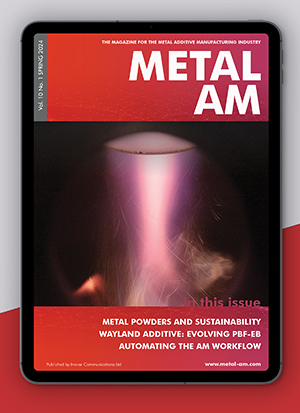