USS San Diego pilots ADDiTEC’s liquid metal jetting technology
April 30, 2024
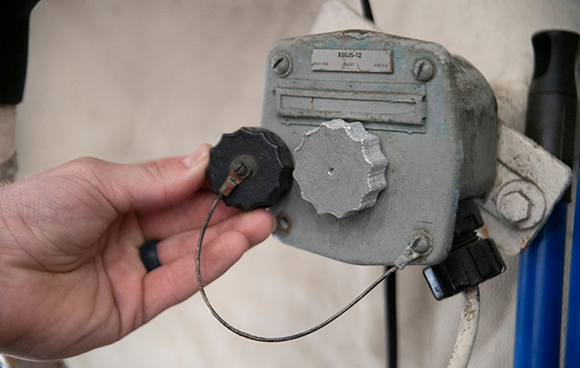
Amphibious Transport Dock USS San Diego (LPD 22) sailors have reported operational testing of ADDiTEC’s ElemX liquid metal Additive Manufacturing machine for the fleet. The USS San Diego is reportedly the first San Antonio-class LPD warship to test the machine’s on-site AM capabilities. The ElemX machine sits inside a 6.1 m self-contained unit in the ship’s main vehicle stowage area.
“The purpose of the 3D printer is to establish an Additive Manufacturing capability aboard L-Class ships,” stated Chief Warrant Officer Nicholas Garcia, US Marine and Combat Cargo Officer. “This reinforces our ability as a naval force to implement self-help measures from an engineering casualty perspective and to confront future landing force maintenance requirements. These are necessary to project combat power during crisis response and contingency operations.”
In August 2023, ADDiTEC obtained the the ElemX liquid metal technology when it acquired Elem Additive Solutions from Xerox Holdings Corporation. The liquid metal process falls broadly into the ISO/ASTM 52900:2015 category of Material Jetting, using widely available aluminium wire as the primary feedstock. The process uses molten metal droplets to create three-dimensional objects layer by layer. Unlike traditional metal Additive Manufacturing methods, such as powder-based techniques or directed energy deposition, the process employs the unique properties of liquid metals to achieve high-resolution and intricate metal parts.
On-site liquid metal Additive Manufacturing aims to address the supply chain gap between the manufacturer and the customer.
“It can take a long time to receive certain parts in the Navy,” shared Aviation Boatswain’s Mate (Fuel) 1st Class Christopher Robertson. “With something like this, we can turn six months of waiting for a part into a couple of hours.”
San Diego’s air department sailors were amongst the first to receive AM training. Aviation Boatswain’s Mate (Handling) 2nd Class Scott Kibler recalled that the learning of the operation of the AM machine itself was fairly simple and that air department Sailors have attended multiple classes to learn the machine’s operation.
“It is significantly different from anything else I’ve done in the Navy mainly because you aren’t ordering a part from a manufacturer,” he said. “You have to use real-world skills to reverse engineer the part or make a 2D drawing, then a 3D model, and print it. You have to be so precise to ensure it fits into the system correctly.”
Since initial training began, air department sailors have created low-pressure air fittings, toggle pins, sound-powered phone caps, and flush deck nozzle covers.
“The 3D printer is envisioned to reduce in size in order to make it a permanent work space aboard L-Class ships,” Garcia commented.
Whilst the USS San Diego is currently the test bed for Additive Manufacturing in the fleet, it is anticipated that AM will eventually be a reality on all L-class ships in the fleet.
In April 2024, the Naval Postgraduate School worked to establish itself as a driving force in Additive Manufacturing research and education for the US Navy, US Marine Corps and Department of Defense, especially for applications in operational environments. Now the institution is taking another step forward in the realm of AM, establishing a new laboratory to pursue further breakthroughs in AM and related technologies for defence applications.
Download Metal AM magazine
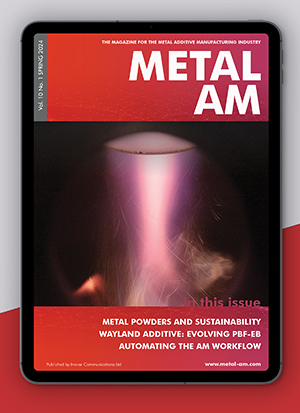