AIM3D technology used to produce conformally cooled tooling for MIM
July 21, 2023
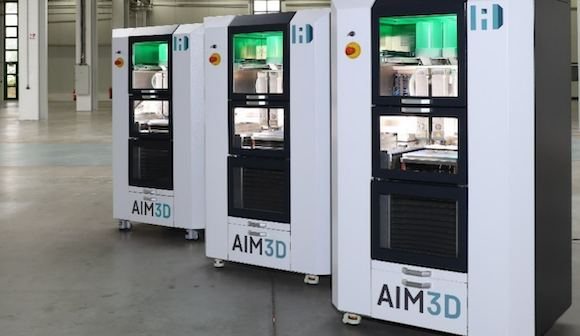
The Chair of Microfluids at the University of Rostock has collaborated with Metal Injection Moulding (MIM) producer Stenzel MIM Technik GmbH, headquartered in Tiefenbronn, Germany, to create an additively manufactured MIM tool with AIM3D’s ExAM 255 machine.
The machine uses what AIM3D refers to as Composite Extrusion Modelling (CEM), in which MIM feedstock-like pellets are extruded in a similar way to a filament in filament-based Material Extrusion (MEX), also called Fused Filament Fabrication (FFF). CEM, it is claimed, brings the advantage of high precision and high build speeds.
“Composite Extrusion Modelling by AIM3D is an Additive Manufacturing process that uses feedstocks consisting of plastic binders and metal powders known from Metal Injection Moulding. With this process and after the necessary debinding and sintering steps, complex metallic components can be rapidly produced,” explained Dr Abdullah Riaz, research associate at the Chair of Microfluidics at the University of Rostock.
The project, funded by the German Federal Ministry for Economic Affairs and Energy (BMWi) and due to be completed by October 2023. The aim is to use the technology to manufacture a MIM tool with near-contour (conformal) cooling to reduce the injection moulding cycle time. Such cooling can lead, in particular, to a faster demoulding process.
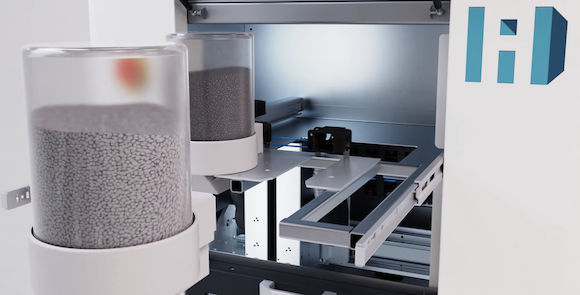
“The aim of the cooperation project is to develop a digital process chain for the cost-efficient and rapid production of MIM tools. Up until now, periods of up to eight weeks are needed to produce a MIM mould. This project aims to reduce the provision time to about five days,” Dr Riaz added.
The complex geometry of the helical cooling channels is created using CAD technology which utilises simulation models based on the ‘needs’ of the component. Long-term experience reportedly shows a reduction in cycle time of around 20%, depending on wall thickness and size. An optimised 3D model of the tool was initially developed using CAD and simulation tools. This data was then transferred to the ExAM 255 CEM system, together with the necessary process parameters, in order for a ‘green part’ to then be manufactured. The tool is then sintered to achieve the final material properties.
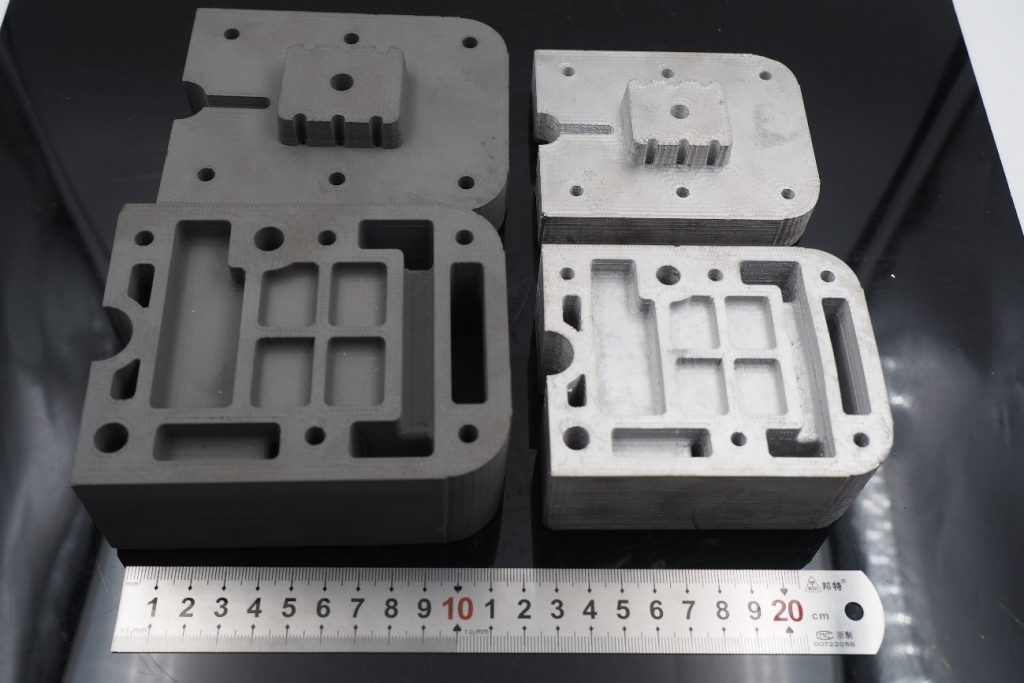
The MIM component for which the AM tooling is being developed consists of a thick-walled part with thin fins that cannot be efficiently moulded without conformal cooling. Stenzel MIM Technik hopes to achieve a significant reduction in cycle time for this component – by up to 70-80%. However, injection moulding trials for testing are still pending.
Riaz commented “With the CEM process, both material and machine costs can be reduced and at the same time the problems of Additive Manufacturing with regard to residual stresses and material adjustments on the individual machines can be avoided. This innovative solution allows tools to be produced four to eight times faster and at the same time more cost-efficiently.”
Download Metal AM magazine
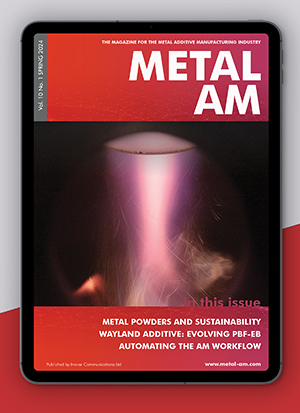