US Air Force selects Essentium to accelerate deployment of Additive Manufacturing
October 28, 2020
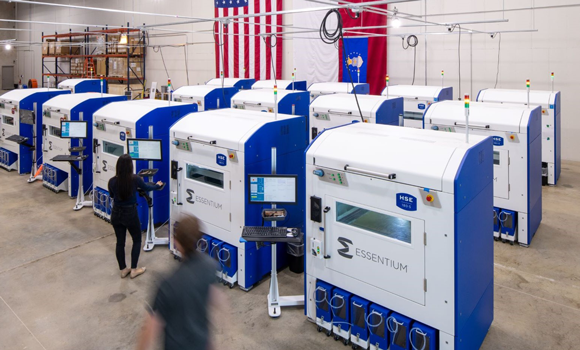
Essentium, Inc., Austin, Texas, USA, has been awarded a contract by the US Air Force to drive the development and deployment of advanced Additive Manufacturing solutions for applications in tooling, ground support, maintenance repair and overhaul (MRO), and flight-certified parts for military aircraft and ground vehicles through both the US Air Force and the National Guard Bureau (NGB).
The multi-year collaborative contract is thought to have the potential to save both services millions by ramping up AM production and developing certified materials that will produce consistent quality AM parts at unparalleled speed and economics.
The contract is part of more than $550 million recently deployed through the inaugural Strategic Financing (STRATFi) initiative to identify and advance technologies that have the potential to protect and advance the US Air Force and its airmen. The contract will also help the NGB advance its ability to speed the production of parts for ageing fleets of air and ground vehicles.
For many ageing aircraft, replacement parts are scarce, and, using conventional production methods, it is challenging to find manufacturers willing to resume the production of parts that may not be reordered for many years. Parts ordered one or two at a time for production by conventional methods are extremely expensive and lead times very long, forcing the US Air Force to turn to ex-service parts from the ‘aircraft boneyard’ at Davis-Monthan Air Force Base, Arizona.
Using Additive Manufacturing enables replacement parts to be produced with much shorter lead times and at lower cost, thus addressing these production, supply chain, and procurement challenges. The Essentium-US Air Force project team will test and develop new materials and processes using the Essentium High Speed Extrusion (HSETM) 3D Printing Platform, a Material Extrusion (MEX)-based Additive Manufacturing machine, said to offer build speeds useful for both rapid part production at the point of use and decreasing the time required to certify new materials for use in flight.
Essentium engineers will use their knowledge and experience in materials science to offer drop-in replacements for military grade materials. The team will reportedly aim to certify 4X the quantity of materials in significantly less time and cost compared with incumbent solutions currently available to the US Air Force.
Nathan Parker, Deputy PEO, Rapid Sustainment Office, US Air Force, stated, “Developing safety-critical airplane parts is closer than ever before due to cutting-edge technology like Essentium’s Additive Manufacturing solution. Essentium demonstrated it has the expertise and capabilities to create parts with consistent replication using the Essentium HSE 3D Printing Platform. We will work together to drive Additive Manufacturing technology forward; for faster aircraft repairs that massively reduce time to deliver parts to keep our war fighters ready.”
Elisa Teipel, PhD, Chief Development Officer and co-founder of Essentium, Inc. commented, “The sky is the limit for the potential benefits of Additive Manufacturing for the US Air Force. As well as reducing operating costs by tens of millions, the strategic capability we will work with our STRATFi partners to deliver through this programme will help bring about an end to the scenario of days of aircraft sitting on tarmac awaiting simple replacement parts which may be 3D printed and can get them flying again.”
“We are beyond thrilled to be awarded this contract and work with our government customers to help drive significant advancement in military parts manufacturing and advance the US Air Force’s military leadership,” she concluded.